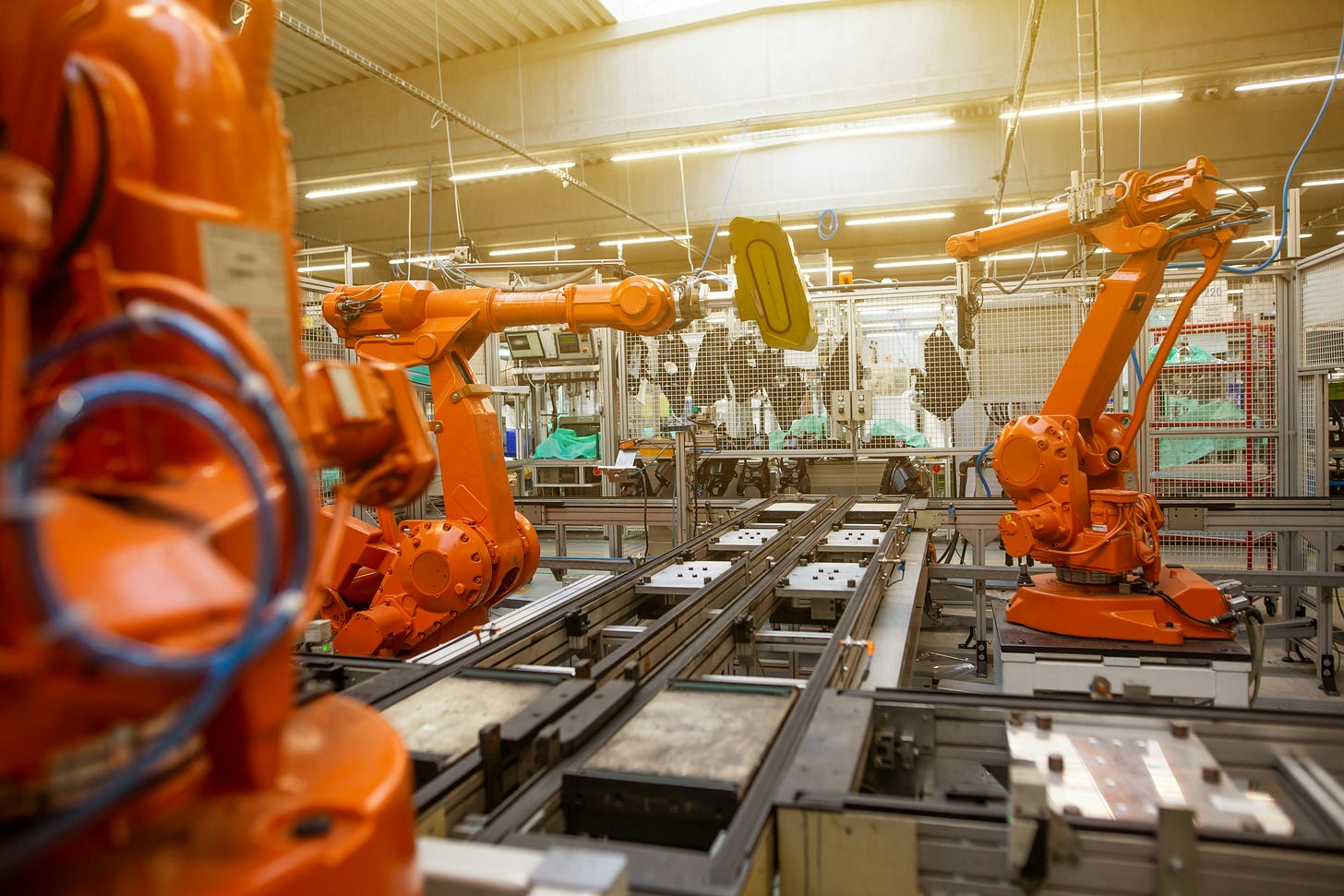
A future where U.S. manufacturing employs more people than it does today is unlikely.
For decades, automation, not off-shoring, has been the primary driver in the shifting landscape of manufacturing employment in countries like the U.S. This trend of machines taking over manual labor is not new; it's a centuries-long progression. The main hurdles slowing full automation have always been the high cost, especially for retrofitting existing plants, and the uniquely human ability to make nuanced judgments and adapt to unforeseen variability—tasks machines struggled with.
Until now. The arrival of Generative AI is dismantling these final barriers. AI can now increasingly make more difficult judgments and adapt to dynamic situations, fundamentally changing the equation.
Full-scale “lights-out” factories, operating with minimal or no human presence on-site, are already a reality, particularly in sectors demanding extreme precision and high volume. They are usually for semiconductor fabrication, where dust-free cleanrooms are run by robots, or the mass production of consumer electronics. These environments are hyper-controlled, requiring immense capital investment and unwavering consistency.
However, most manufacturing operations have historically been considered too variable, too "messy," or simply too costly to automate from end to end.
Automation was a tough nut for industries like food processing, where deboning chickens (each one unique!) was a real challenge for old-school robots. The same went for apparel and textiles; fabric is so pliable and varied, it totally stumped rigid machines. And if you were doing small-batch or custom jobs and weren't mass-producing? Automation often cost too much.
But AI is starting to change the game.
Why True Automation Was So Hard
It’s easy to underestimate the degree of variability and complexity humans deal with effortlessly . Parts arrive with slight imperfections. Lighting conditions shift. Raw materials, from metal sheets to agricultural products, are never perfectly uniform. A pallet of components might contain subtly damaged packaging. A piece of raw meat, for example, is unique every time. Traditional robotics, programmed for repetitive, exact tasks, often falter when faced with such real-world inconsistencies.
Historically, many robotic systems demanded highly structured environments and explicit, line-by-line programming. While more advanced systems incorporating machine vision, fuzzy logic, and early forms of machine learning have been present in manufacturing for decades, they lacked the broad adaptability of Generative AI. Reprogramming these older systems for a new product or a different configuration meant costly downtime and specialized engineering talent. Consequently, automation often remained confined to specific, predictable tasks like welding, painting, or simple pick-and-place operations, predominantly in sectors with highly standardized inputs. This is why so many factories still rely on human workers to bridge the gaps between what machines can do.
The "Reliability" Red Herring
A common critique of Generative AI is its potential unreliability—its tendency to "hallucinate" or generate incorrect information. In fields like medicine or legal advice, these are critical concerns. However, in many manufacturing contexts, the nature of the "questions" AI needs to answer is different: Can this robot identify and grasp an object from a cluttered bin? Can it distinguish between different components? Can it place an item correctly and safely?
Here, GenAI doesn’t need to achieve abstract perfection. It needs to be more flexible, adaptable, and cost-effective than legacy automation and on par with people (who also make mistakes). In many emerging applications, it already is. Recent AI models are empowering robots to navigate unstructured environments, understand object occlusion (when one object blocks another), plan actions around uncertainty, and even learn from their mistakes. High performance isn't just about being reliable, but also about being resilient and versatile.
What’s Different Now?
Generative AI isn't a magic bullet, but it fundamentally shifts the dynamics of automation. For instance, advanced vision capabilities, powered by AI models like Segment Anything Model (SAM) or DINOv2, enable robots to "see" and interpret complex, cluttered scenes with near-human acuity, identifying and segmenting objects even in unpredictable environments and from few examples. Other AI technologies facilitate adaptive movement, allowing robots to learn and adjust their physical actions in real-time, much like a human would, rather than rigidly following pre-programmed paths. And importantly, large language models (LLMs) are paving the way for easier interaction, creating more intuitive ways to instruct, reconfigure, and manage robotic systems, which reduces the need for deep technical expertise to make adjustments. LLMs also accelerate the development and testing process via code generation.
In practical terms, these AI advancements are driving towards robots that can handle a much wider array of product variations (SKUs) and adapt to new tasks with significantly less manual reprogramming by engineers. This increased flexibility and reduced need for task-specific programming is a central theme in the application of modern AI to robotics. This is a significant breakthrough, particularly for industries with diverse product lines.
These advanced systems are no longer confined to research labs; they are appearing in real-world factories. For example, Tyson Foods is actively deploying and investing heavily in AI-driven robotics for tasks like meat deboning, tackling the variability of natural products. In the apparel sector, robots are demonstrating the ability to handle complex tasks like T-shirt assembly, a major step in automating apparel manufacturing. Meanwhile, electronics giants continue to push the boundaries of automation in their facilities, investing billions in robotics and AI to enhance efficiency and precision in producing everything from semiconductors to, increasingly, components for electric vehicles.
Even smaller manufacturers, traditionally unable to afford or implement complex automation due to high product mix and lower volumes, may soon find AI-driven robotics within reach. GenAI lowers the threshold for what is considered automatable.
So, Will the Jobs Vanish?
A lot of them will. The types of labor most vulnerable are those that are highly repetitive, manually intensive, and physically constrained. The roles that remain, or evolve, will likely involve system oversight, complex problem-solving for edge cases, design and development of automated systems, and tasks requiring a level of intricate, non-repetitive physical dexterity that AI has yet to master (though this boundary is constantly shifting). But the number of jobs will be lower, and even the supervisory work may be automated to a large degree in future tech iterations.
In niche areas—such as small-scale artisan production or culturally specific crafts—human labor may retain its preference or economic viability. But across the broad landscape of industrial manufacturing, the decades-long trend towards reduced direct human labor is not only continuing but accelerating, thanks to AI. The value of human contribution is shifting "up the stack"—towards configuring and managing these intelligent systems, driving innovation in products and processes, and ensuring the overall system works effectively.
The Shifting Economics of Automation
Beyond capability, there's the ever-present and decisive factor of cost. Automation has always been pursued to enhance productivity and manage labor expenses. For many years, certain manufacturing roles persisted simply because automating them was too expensive or the available technology wasn't flexible enough to provide a return on investment.
AI is changing this economic calculation. One major factor is software accessibility; sophisticated machine vision, motion planning, and control logic once required extensive, custom engineering from a sparse labor pool. Today, many of these functionalities can be powered by pre-trained or fine-tunable AI models, dramatically cutting development costs and time. Another aspect is the rise of more versatile hardware, as robotics hardware itself is becoming more standardized and general-purpose. Collaborative robots (cobots), adaptable gantry systems, and autonomous mobile robots (AMRs) can be repurposed for various tasks with less need for complete overhauls, and this flexibility allows for mass production of robotic components, driving down unit costs. Finally, there's a flattened learning curve; the expertise and time required to deploy and integrate robotics are decreasing thanks to more modular systems, advanced simulation tools, and established frameworks, a process AI further simplifies by enabling systems to learn and adapt with less explicit programming. The lower learning curve means the historical skill constraints are alleviated.
As a result, the return on investment for automation is improving, especially when juxtaposed with rising wages or labor shortages in some regions. Tasks that were once technically automatable but economically marginal are now decisively tipping into the feasible zone.
All this unfolds against a political backdrop where the return of domestic manufacturing jobs is a common promise. However, the dual forces of rapidly increasing AI capability and falling automation costs are pushing firmly in the opposite direction. Factories may indeed be built or re-shored, but any new, competitive manufacturing facility will inevitably be highly automated.
Because of AI, traditional manufacturing jobs, in the form and number they once existed, are not coming back. The labor share of production has been on a long-term decline, and AI is set to continue, and likely quicken, that trajectory.
The critical question now is how we prepare our workforce and society for this evolving reality.
©2025 Dasey Consulting LLC
Tim, your analysis in “Because of AI, Manufacturing Jobs Aren’t Coming Back” is both sobering and essential reading. At IntelliSell, we’re witnessing firsthand how AI-driven automation is reshaping the manufacturing landscape—not just in terms of technology, but in workforce dynamics and economic structures. 
Your point about the diminishing role of labor cost advantages due to AI advancements resonates deeply. As AI systems become more adept at handling complex tasks, the traditional incentives for offshoring are eroding, leading to a reevaluation of manufacturing strategies globally. 
Moreover, your emphasis on the need for a paradigm shift in education—from rote learning to fostering adaptability and critical thinking—is crucial. Preparing the workforce for an AI-integrated future requires not just technical training but also the cultivation of uniquely human skills that machines cannot replicate. 
Thank you for shedding light on these critical issues.
—IntelliSell Team
Transforming market noise into strategic intelligence for manufacturers